The Importance of Measurement in Manufacturing
It goes without saying that correct dimensional measurement is a key factor in manufacturing. Performing measurements with the same reference throughout all processes—from material reception to processing, assembly, inspection, and shipping—makes it possible to create products that match the design exactly and to guarantee product quality.
If even one person performs inaccurate measurements, product quality can be compromised. Should this lead to defective products being mixed in with good products, the result will be a worse yield. In addition, shipping defective products as finished products will lead to complaints from customers. In other words, it is essential that all members of an organisation perform correct measurements throughout every step of the manufacturing process.
The basic principle for correct measurements is to ensure that all those involved in manufacturing are skilled in measuring, and that the measuring instruments are correctly managed and used. These basics make up an initiative known as "Measurement Control," which is a core concept of quality control. In recent years, measurement control has been standardised as measurement management systems (ISO 10012). Also, initiatives for metrological traceability have been proceeding steadily in order to guarantee correct measurements.
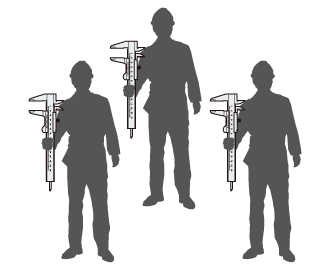
- Measurement System BasicsWhat is Measurement?
- Measurement System BasicsDirect and Indirect Measurements