Industrial Laser Marking Systems / Laser Markers
Laser Marking—Ensuring the Safety of Medical Device Applications Worldwide
-
Tags:
- Medical , Laser Labeling , Laser Annealing
Medical devices are crucial tools in the healthcare world used to diagnose, prevent, or treat various conditions and diseases. They are categorised as Class I, Class II, and Class III. These rankings show how necessary the device is to sustain life. Since medical devices are life-altering, they follow strict regulatory guidelines to ensure safety and quality. Medical devices require permanent traceability marks that are read by humans and computers.
To keep compliance with regulations and ensure safety, using laser marking is an optimal choice for marking medical devices. Laser markers are user-friendly machines that produce Grade A marks that don’t wear over time or require consumables.
In this article, we’ll discuss how laser marking for medical devices ensures traceability, anti-counterfeiting, and compliance, and how to achieve laser marking safety.
Importance of Traceability in Medical Devices
The International Organisation for Standardisation (ISO) defines traceability as “the ability to trace the history, application, use and location of an item or its characteristics through recorded identification data.” All industries follow this practice, and although every industry needs traceability, it is particularly important for medical devices because of life-threatening implications. Medical devices are used on patients, usually in vulnerable situations, so it is necessary that medical devices have a trackable history to solve any problems before their consequences. As such, laser marking becomes an essential process, which makes laser marking safety a necessity.
We’re here to provide you with more details.
Reach out today!
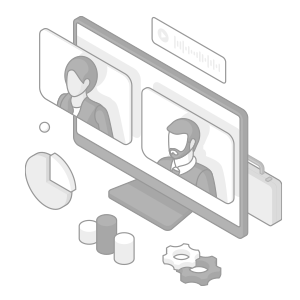
Benefits of Implementation
Managing medical equipment through direct marking offers the following advantages.
- Maintenance of quality by being able to monitor how frequently tools are used
- Optimisation of replacement and order timing
- Improvement in efficiency and standardisation of instrument sets
- Tracking of instruments during each process (location management)
- Prevention of excess stock
- Analysis of loss and theft, etc.
Curious about our pricing?
Click here to find out more.
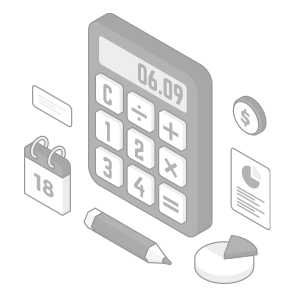
Explanation of Anti-Counterfeiting in Medical Devices
Medical devices follow a strict regulation process to ensure the best quality for patients and healthcare professionals. However, some counterfeiters use cheap labour and cheap materials to fraudulently sell imitation products, which threatens the integrity of devices and the safety of patients.
Counterfeit products are hard to spot, as they are made to look identical to the regulated product. Because of this, it is possible healthcare professionals could accidentally use a defective, counterfeit product that breaks, produces inaccurate results, or threatens a patient’s life. Counterfeit products cannot be traced back to a manufacturer, so fixing the defective product is impossible.
With the FDA’s unique identification system (UDI) and Access Global Unique Device Identification Database (AccessGUDID), healthcare professionals and manufacturers can check the validity of their devices before use. If manufacturers, importers, or device user facilities notice a medical device malfunction that could cause death or serious injury, they must report it to the FDA with the Medical Device Reporting (MDR) tool. Proactively addressing counterfeiting issues with a laser marking system is the best way to ensure UDI laser marking safety and MDR laser marking safety.
Regulatory Requirements for Medical Device Markings
UDIs are used for most medical devices, but not all. The FDA concluded that all medical devices need UDIs except for consumer health products. Consumer health products are class I devices that are sold over the counter directly to customers.
For devices required to display a UDI, manufacturers must follow a few regulations.
- The UDI must appear on the device’s label or package
- The UDI must be readable by a machine and a human
- When a UDI is added, the corresponding device data must be added to the FDA Global Unique Device Identification Database (GUDID)
UDIs fall into two categories: device identifiers and production identifiers. Device identifiers signify what type of instrument the product is. Production identifiers store information like serial number, batch number, expiration date, and manufacturing date.
When adding UDIs to a medical device, choosing a laser marker is key to ensuring long-term compliance. Laser marking easily creates UDIs that appear clearly on labels and packages. UDIs by laser markers are also readable by machines which makes them easy to track and evaluate for counterfeiting.
We’re here to provide you with more details.
Reach out today!
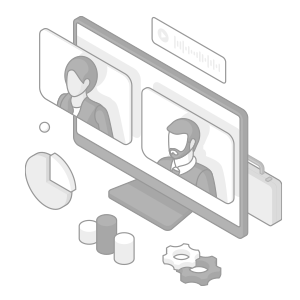
Benefits of Laser Marking for Medical Manufacturers
Clean and Permanent Marks
Using a laser marker for UDIs ensures clean and permanent traceability marks that follow FDA compliance. The FDA requires UDIs to be readable by both a machine and a human, so marks must be precise, clean, and permanent. Laser markers use high energy light to mark the surface of a part through thermal or photolytic degradation, depending on the wavelength of the laser. The KEYENCE MD-X Hybrid Laser can provide manufacturers with a Grade A level compliant mark, as well as grade the resulting mark to assure it’s quality.
Laser markers outperform printing and stamping for UDIs because there is no use of ink. Using ink can cause issues because it can disintegrate, smudge, or erase over time—inevitably becoming non-compliant with the UDI readability standards and appearing counterfeit. The marks created by laser markers withstand heat, friction, and frequent sterilisation. Additionally, the marks do not rust or require consumables.
Mark Difficult-to-Reach Areas
Many medical devices, like tubes, catheters, and screws, are odd shapes with limited marking areas. Nevertheless, these medical devices are still required to have UDIs. Fortunately, because of the use of the precise laser beam, laser markers can mark medical devices of any shape, size, or marking area.
Particularly with KEYENCE’s laser markers, there are features that ensure distortion-free marking. KEYENCE’s laser markers have a 3-axis control that auto-adjusts its focal distance based on the product positioning. Additionally, KEYENCE’s laser markers contain software that sets up a foundation for three-dimensional marking. With this software, manufacturers can remotely align the UDI onto the 3D medical device without distortion.
Steps
Inclined Surface
Cylinder
Circular Cone
Easily Create 2D Codes
Using a 2D code as a UDI on a medical device is a good choice because of how much information can be stored inside. Laser markers can easily create these codes using black annealing, white engraving, or both in one process.
KEYENCE's lasers are especially proficient when it comes to 2D code marking. The 3-axis ability of their laser marker makes it possible to mark different or difficult geometries while staying in focus, which is essential for a clean and uniform 2D code. There is also a built-in 2D code reader that adds the ability to mark, read, and even grade the 2D code with one piece of equipment. This assures the marks are high quality and reduces scrap from poor marking.
Safely Mark
Ensuring laser marking safety and UDI laser marking safety is a top-tier priority. Using a laser marker for medical devices can be completely automated and could take place exclusively inside a cell. With KEYENCE's lasers, there is no need for physical adjustments because of the autofocus technology of their lasers. Setting up a production project can happen remotely using a laser marker’s built-in software. Also, laser marking requires no consumables, which avoids the potential for contamination by manufacturers.
Examples of Medical Device Manufacturing
Medical device manufacturing includes designing, manufacturing, fabricating, assembling, and processing devices. When achieving UDI laser marking safety, there are inspection and automation solutions for medical device manufacturing. Examples are the use of an autofocus 2D code reader, electrostatic eliminator, and digital microscope.
Discover more about this product.
Click here to book your demo.
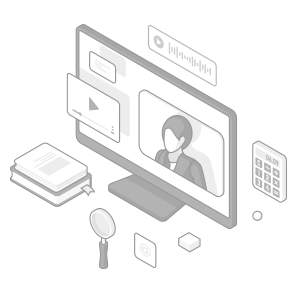