Industrial Laser Marking Systems / Laser Markers
Laser Spot Welding vs Laser Seam Welding
-
Tags:
- Medical , Semiconductor , Battery
Lasers are a well-known tool in the manufacturing world, not only for marking but also for outperforming traditional welding. Laser welding is versatile and sturdy, joining thick, thin, and dissimilar materials. The lack of heat transfer means that laser welding doesn’t just tackle metal—it welds resin, too.
There are two types of laser welding: laser spot welding and laser seam welding. Both welding methods are the way they sound; spot welding is in a specific area or “spot,” and seam welding is overlapped welded spots that follow a seam. For comparison, think of clothing buttons versus zippers—both are successful for holding two fabrics together but are not appropriate for every scenario.
These methods are reliable and produce effective welds, but they have benefits specific to each of their welding processes. In this blog, we’ll dive into the specifics of laser seam welding vs spot welding and how to choose one over the other.
What is Laser Spot Welding?
Laser spot welding is a precise welding method that uses slow pulse beams to bond a material to a specific area. This technique is commonly applied to materials that don’t require full adhesion but instead involve specific part welding. For instance, spot welding is used to attach a small connector to a semiconductor wafer. In this case, the connector is only being welded to a specific spot on the wafer, not the whole wafer.
We’re here to provide you with more details.
Reach out today!
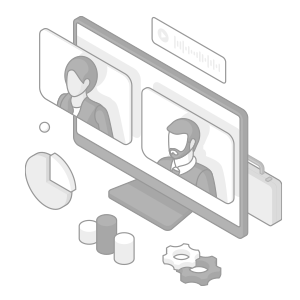
What is Laser Seam Welding?
Laser seam welding incorporates the spot welding technique, but instead of targeting one area, the spots are welded along a continuous seam. This technique uses a laser with a continuous or rapid pulse beam. Since laser seam welding covers a larger area, it provides more strength and coverage.
Discover more about this product.
Click here to book your demo.
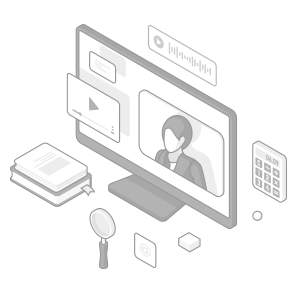
Benefits of Laser Spot Welding
Energy Efficient
Laser spot welding is energy efficient because it bonds materials in less time and energy than seam welding. Instead of welding an entire component, spot welding is specific to one area and doesn’t need to be applied all over.
Localised Welding
Laser spot welding only focuses the laser on one area of a component, yet still successfully welds together. The localised welding aspect means that laser spot welding is achievable on sensitive components and doesn’t disrupt electricity or other functions.
Fewer Cracks
Laser spot welding is less susceptible to cracking from the weld. Since the weld doesn’t adhere as tightly as a seam weld, the material has room to breathe and doesn’t crack under pressure.
We’re here to provide you with more details.
Reach out today!
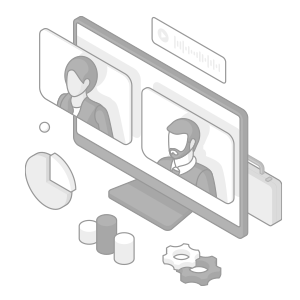
Benefits of Laser Seam Welding
Ultimate Strength
Laser seam welding is welding across a seam—instead of one spot—so there’s a more substantial adhesion between materials. The adhesion strength withstands harsh conditions and pressure, which makes it ideal for applications needing to prevent leakages. The strength also means that seam welding is used in industries with tight regulations and risks, like automotive, aerospace, and medical devices.
No Heat Stress
One would think that the more a beam is used, the more heat stress. But that is not the case. Laser seam welding does not apply any more heat stress than spot welding does.
Even though laser beams technically use heat, laser seam welding heat transfer is significantly less than traditional welding methods. Laser seam welding successfully sticks materials together without damage even though the beam moves across a large area.
Precise and Clean Lines
Precision is a constant in laser processing, and seam welding is no different. Laser seam welding maintains precision along seams without deviating.
Lightweight
Using laser seam welding helps manufacture lightweight aircraft and automobiles. Instead of using heavy steel nuts and bolts, using seam welding gives the same security without the extra weight.
Curious about our pricing?
Click here to find out more.
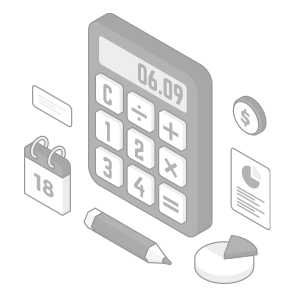
Applications for Different Welding Techniques
Laser spot welding and laser seam welding work together in industries like automotive and EV batteries, but they each shine on their own in the oil & gas and semiconductor industries. When deciding between laser welding techniques, consider the sensitivity of your components and the required level of tightness for the weld.
Oil & Gas
The oil & gas industry uses plant piping that stores water, sewage, gas, and powders. These pipes are pressurised and face harsh environmental changes like severe weather, rust, and vibration. But, if these pipes burst, human and environmental health is at stake. Because of the severity of leakage, laser seam welding is a reliable method for sealing pipes to prevent leaks.
Semiconductor/Electronics
Semiconductors are made up of tiny components, each serving an electrical function to ensure the semiconductor works correctly. Some semiconductors have dozens of layers. With all the layers, the components must be welded one at a time and without contamination.
Since each component must be placed per spot, laser spot welding is ideal. Laser spot welding allows for each component to be placed without affecting anything else around it or threatening the integrity of the semiconductor.
Automotive
The automotive industry benefits from spot and seam laser welding techniques.
Laser seam welding succeeds at tight and long welds that assemble vehicle frames. The seam follows the frame’s outline and bonds the thick metal components together. The strength of laser seam welding is also used for sealing gunpowder for airbags. When an airbag goes off, the weld keeps the gunpowder in while inflating the airbag.
The automotive industry also uses spot welding for smaller welding needs. Laser spot welding works well for adding adhesion to nuts and bolts.
EV Batteries
Laser seam welding is used for stacking electrodes to make prismatic and pouch batteries. The tight weld between electrodes creates a strong bond between layers, so energy flows smoothly.
Once the electrodes are stacked to form a battery, laser spot welding is used to bond the batteries inside the battery pack and make specific connection points.
Choosing a Laser Machine for Welding
The most popular laser machine for welding is a CO2 laser marking machine. CO2 lasers generate laser beams from CO2 gas and plasma to produce a 10600 nm wavelength. CO2 lasers are ideal for welding plastics, resins, or films.
Fibre laser marking machines are also used for laser welding. A fibre laser generates its laser beam with a fibre oscillator and produces a 1064 nm wavelength. The wavelength can be used continuously or for ultra-short pulses. Fibre lasers are known for speed and power, so thick metals and large projects benefit from fibre laser welding.
We’re here to provide you with more details.
Reach out today!
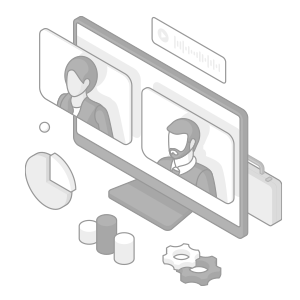
KEYENCE’s Laser Welding Machine
Laser seam welding and spot welding are versatile options for many manufacturing processes. However, some features make each welding technique optimal for various reasons. Choose seam welding if you’re looking for a tight weld that holds components into place even when faced with pressure. But if you want welding in only one area, choose laser spot welding.
Regardless of which technique is right for you, KEYENCE offers CO2 and fibre laser marking systems that act as a laser welding machine for both techniques.
Our lasers are made for your unique applications and include 3-axis control to weld any shape. The 3-axis control auto-adjusts the focal point so the laser beam moves beyond a single plane. Whether you plan to seam weld in a curved pattern or spot weld a connector to your semiconductor, our lasers are flexible enough to complete the task. Test out which technique works best for you—request a demo today.
Discover more about this product.
Click here to book your demo.
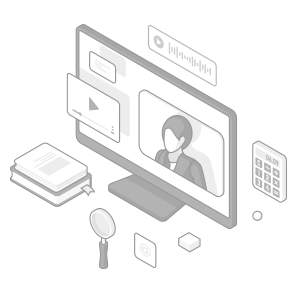