Industrial Laser Marking Systems / Laser Markers
What is Laser Cutting? A Guide to the Process & Methods
-
Tags:
- Laser Cutting , Laser Ablation , Medical
Throughout industries, various methods are used to precisely create cuts and ensure products adhere to specifications. For many, lasers play a pivotal role to help manufacturers and businesses save time and money. In the following, we’ll look at how laser cutting is often a great choice.
What is Laser Cutting?
Laser cutting is a contactless cutting method that uses a laser beam to melt or evaporate the target area.
Cutting
Cutting is when a material is fully sliced through to separate it. For example, cutting a steel blank into two slabs.
We’re here to provide you with more details.
Reach out today!
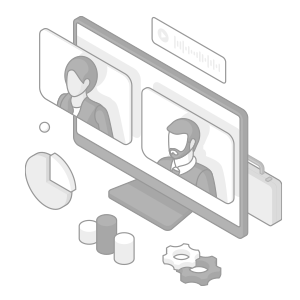
What Lasers Are Used for Cutting?
CO2 Laser
A CO2 laser cutting machine is powered by processing CO2 gas in a tube, turning it into plasma between a reflexive mirror and an output cooler, then shooting it onto a material’s surface. The target surface absorbs the light once the laser beam hits the material.
Hybrid Laser
A hybrid laser cutting machine combines a fibre laser’s amplifier technology and the high-quality beam of a YVO4 laser oscillator.
These lasers bring their best qualities together. Combined, the hybrid laser reaches a peak power two times that of a conventional YVO4 laser. This high peak power is used with short pulses, minimising heat damage during the cutting process.
Discover more about this product.
Click here to book your demo.
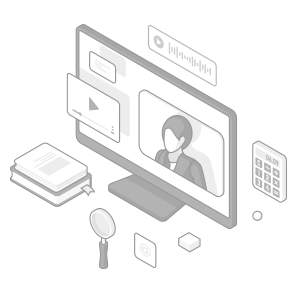
Laser Cutting Process
CO2 Laser Cutting Process
A CO2 laser cuts by shooting out a power-dense small spot diameter beam onto a surface to absorb part of the material. The absorbed material disintegrates and leaves behind a clean cut. The high absorption rate of the CO2 laser makes it ideal for cutting film, plastic, resin, and other reflective materials.
Hybrid Laser Cutting Process
Hybrid lasers cut by shooting the surface with high peak power and short pulses. This laser cutting machine process is ideal for thin metals due to the wavelength and absorption rate of the hybrid machine.
Here are some common applications, materials, and industries that work well with this process:
Laser Cutting Materials | Laser Cutting Industries |
---|---|
Laser Cutting Industries
|
We’re here to provide you with more details.
Reach out today!
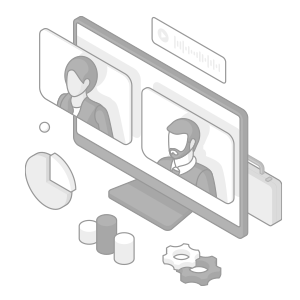
Laser Cutting Applications
Laser Cutting Cable Sheath
Cutting cable sheaths can be risky. The wrong cutting tool can slice open the wire core and lead to a wasted product.
Using a laser for cutting instead is a full-proof option, especially for half cuts by CO2 lasers. Since metals reflect CO2 lasers, the wire core will not absorb heat from the laser.
Laser Cutting Wood
Laser cutting wood is a contact-free method that cuts in seconds. Wood is cut with no ragged edges. This method outperforms typical wood-cutting methods. The friction makes cutting wood with a tool difficult to cut cleanly.
Laser Cutting Metal
Lasers cutting metal is easy because of the high beam power cutting right through. Also, since laser cutting is contactless, no extra maintenance is required for renewing tools.
Without a laser, cutting metal is no easy feat. Not only does metal’s hardness require intense machinery, but metal wears tools down easily. Tools need to be consistently maintained and sharpened after cutting metal.
Discover more about this product.
Click here to book your demo.
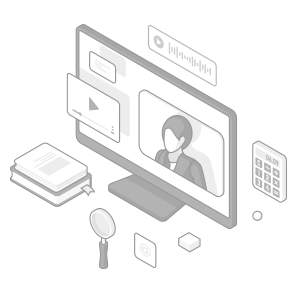
Benefits of Laser Cutting
High Quality Beam Control
One benefit of laser cutting is the ability to handle greater complexity than traditional cutting methods. This accurate beam control allows for intricate designs and is useful in a myriad of industries. For example, medical devices often have intricate geometries and patterns or detailed cuts. Traditional cutting would not be able to maneuver through these obstacles, however laser cutting can due to its high quality beam control.
Efficient
Lasers cut in seconds and easily move down assembly lines. Especially with KEYENCE’s laser cutting service, which includes tilt correction and auto-adjustment, the laser cutting machine process is even faster without tooling changes or manual readjustments.
No Extra Cutting Agent
Hardening of materials sometimes occurs from heavy machining, increasing the friction between a cutting tool and the material. In alternative cutting tools, technicians need to add cutting agents like oil, water, or extra heat. However, a laser cutting machine does not require any cutting agent.
Curious about our pricing?
Click here to find out more.
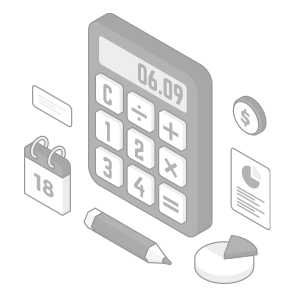
KEYENCE’s Laser Cutting Service
3-Axis Control
The 3-axis control is a KEYENCE specialty in all of KEYENCE’s lasers. This control auto-adjusts the focal point to the target height programmed through marking builder. 3-axis control lessens positioning changeover time and adds flexibility to the laser cutting process.
3-Axis Hybrid Laser MD-X Series
- Peak Power
- KEYENCE’s hybrid laser cutting machine, the MD-X, has a peak power of 200 kW — twice that of a standard YVO4 laser. With this power, the MD-X also uses a short pulse laser with a minimum pulse duration of 4 ns (compared to 100 ns for conventional lasers). The short pulse minimises unwanted heat effects on the target.
- XY Tracking
- The XY tracking within the hybrid laser cutting machine is two built-in cameras that auto-align with the target for precise cutting. The cameras take in the cutting area, so the cameras notice if a target is misaligned and the laser needs to adjust.
- Distance Sensor
- The MD-X laser cutting machine has a built-in distance sensor and light that measures the laser’s distance to the cutting location. The sensor tracks unintentional deviations in height or inclination to prevent any cutting defects. If the machine picks up on tilt or skewed focal point, it can tilt correctly to match the target for precise cutting.
Incorporating KEYENCE’s Laser Cutting Service
At KEYENCE, our machines are versatile, fast, and powerful. Our ML-Z or MD-X laser cutting machine can make clean cuts regardless of friction or material hardness. Our industry-wide knowledge and team offer expert advice for choosing the best laser cutting machine for your needs. Ask KEYENCE today about seeing an in-person demo.
Get detailed information on our products by downloading our catalogue.
View Catalogue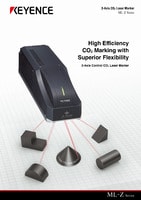
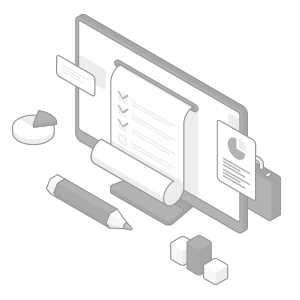